Is it really possible to make 650 hp from a B18C?
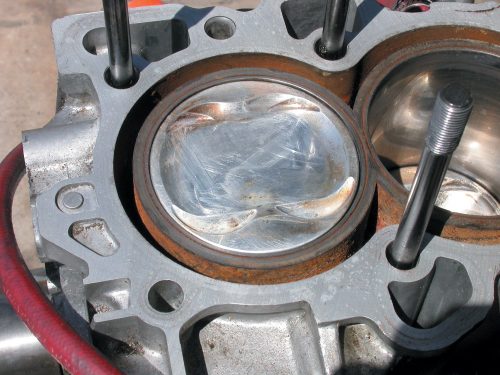
Previously, we detailed the buildup and dyno test of a 475hp turbo B16A (“Boosted B-Series,” p. 50). Designed for street use, the turbo B16A represented what could be accomplished by combining an efficient normally aspirated motor with the benefits of turbocharging. By taking an already healthy normally aspirated motor, we had a head start to producing big power once we upped the boost pressure with our Innovative T04E-46 turbo. But what is necessary to take power to the next level?
The next level we refer to is the kind of sick power found only on the racetrack. Make no mistake, stuffing a 475hp turbo motor in the engine bay of any Civic will make for one wild ride, but we’re talking about crazy turbo power now. If 475 hp isn’t enough to get the party started, how about 500 hp? Still not enough—what about 550? Now things are starting to get serious, don’t you think? But we think we can do even better than 550 hp. Thinking that 600 hp had a nice ring to it, we decided to see what it took to produce over 600 hp from a turbo B-series.
Your first thought may be that all it takes to go from 475 hp to 600 hp is more boost. I mean, if the B16A produced 475 hp at 21 to 22 psi, won’t the power increase with more boost pressure? The answer to that question is actually both yes and no, as additional boost pressure will usually add power, but there is a limit to how much additional power is available from the turbo and how much additional boost will be tolerated by the motor itself.
In terms of the turbo, the T04E-46 used on our 475hp B16A was just about maxed out at the 475hp level. In fact, the power level actually exceeded the numbers indicated by the compressor map, so more power from more boost was not in the cards. Sure, we may have been able to sneak another 25 hp from the combination with more timing, less fuel and a tad more boost, but running the motor on the edge like that is never a desirable situation.
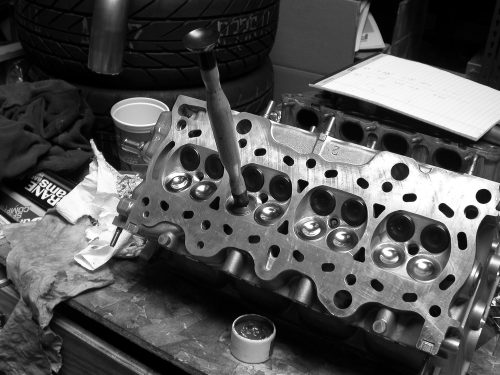
More total timing and a leaner mixture can combine to create havoc in a turbo motor. The same can be said for increasing the boost pressure, since more boost equals more inlet heat, something that again increases the chance of detonation. It should be obvious that more boost is not always the answer when it comes to making more power; however, if more boost is not the answer, then how do we reach our goal of 600 turbocharged horsepower?
One route may be to upgrade the turbo, since we had reached the limit of the smaller T04E-46 on the B16A. While a larger turbo would indeed allow us to increase the power output of the B16A, we would still have to resort to a sizable increase in boost pressure to further the power output of the little B16A. In reality, the turbo wasn’t holding us back from producing 600 hp, nor was the cam timing or the cylinder head flow or the intake manifold. The truth is that the entire combination was at fault, as the turbo B16A was never designed to pump out crazy turbo power. What we needed was to literally start from scratch and build a dedicated 600hp turbo B-series that would allow us to produce the desired power without resorting to astronomical pressure ratios (boost pressure).
The key to producing 600 hp can actually be found in the buildup of the 475hp B16A—at least the basic principles. The success of the 475hp B16A came from the combination of an efficient turbo system with an already powerful normally aspirated combination. This recipe for success holds true even for our 600hp motor. All we had to do was “super-size” both sides of the equation. Stepping up from the 475hp kid’s meal to the super-size 600hp menu required a more efficient turbo system, along with a more powerful normally aspirated motor. Seems simple, right?
Unfortunately, we had already produced a pretty healthy B-series for the 475hp buildup and additional normally aspirated power was getting harder and harder to come by. The key to the additional normally aspirated power came (primarily) for an increase in displacement from 1.6 liters to over 1.9 liters. Simple math told us that the normally aspirated 1.6 liter produced 125 hp-per-liter (200 hp from 1.6 liters). If we retained the same specific output, but increased the displacement to 1.93 liters, the normally aspirated power output should jump to over 240 hp. Adding the proper turbo to a 240hp motor would make reaching our goal of 600 hp much easier and require less ultimate boost pressure.
The first step was to build the larger, more efficient B-series. We started with a 1.8-liter GSR block and had the motor sleeved to increase the wall strength. We did not install a deck insert, as the sleeves have proven more than strong enough to withstand the additional power, providing the motor is tuned to eliminate any trace of detonation. The short block included a stock steel GSR crank, a set of forged Eagle connecting rods and a quartet of forged pistons from Probe Racing. The forged pistons featured dished tops and valve reliefs to lower the static compression while allowing high-lift cams. The short block was assembled using new Honda rod and main bearings and a fresh oil pump. Additional goodies included a set of ARP head studs and a Moroso oil pan that featured a provision for the oil drain for the turbo, which eliminated the need to weld a fitting onto the stock pan. Had the timing been right, we would have run our new Dart block, but we’ll reserve that for a future buildup.
While the extra displacement was a step in the right direction, we knew that additional efficiency would also be beneficial. To that end, we installed one of the new Dart CNC-ported Honda cylinder heads on our turbo motor. The fully ported GSR head featured precision CNC porting on the intake, exhaust and even the combustion chambers. In addition to the porting, the Dart head also featured a complete Ferrea valvetrain, stainless-steel valves, springs and retainers.
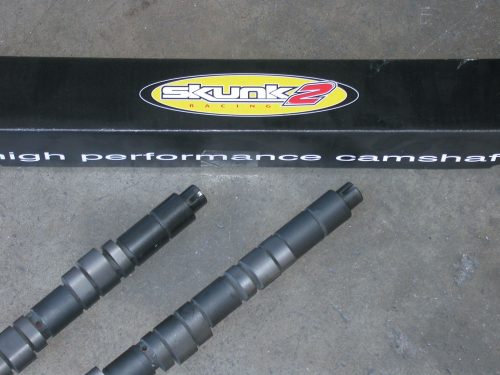
The springs and retainers allowed us to replace the wimpy stock cams with a set of Stage 2 cams from Skunk2. The cams were chosen in an effort to maximize the normally aspirated power. Skunk2 has a reputation for building serious B-series power—its B-series motors have powered winning drag racers, as well as road racers. In addition to the cams, Skunk2 also supplied a set of adjustable cam sprockets (which came in handy to dial in the Stage 2 cams for our turbo application) and an intake manifold to work with the GSR-based Dart head. Compared to a typical P30 (Del Sol or Civic Si) intake, the Skunk2 manifold offered higher flowing ports that allowed our large-displacement motor to produce power up to and beyond 8,000 rpm.
With the 1.93-liter long block coming together, it was time to turn our attention to the turbo portion of the equation. We knew that the T04E-46 turbo used on the smaller 475hp B16A was much too small to produce 600 hp, so we contacted the experts at Innovative Turbo for a suitable replacement. After discussing our combination with Ola Lysentoen from Innovative, we decided on one of its GT72 turbos. According to the compressor map, producing 600 hp at 22 psi would put us in the 75-percent efficiency island. The GT72 wheel was housed inside a 60-1 compressor housing while the T4 turbine side was set up using a Q-trim wheel and 0.81 A/R ratio. The T4 GT72 turbo was supplied exhaust by a custom turbo manifold built by HP Performance in Roswell, New Mexico. The 4:1 tubular header featured 1-3/4-inch primary tubing, a T4 turbine mounting flange and a centrally mounted provision for the wastegate. The use of an Innovative Pro Gate wastegate and centrally located wastegate position provided absolute control over the boost curve.
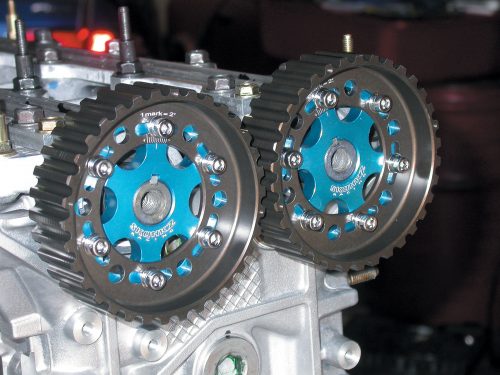
The remainder of the performance components were much like those employed on the smaller B16A. To keep the charge temperature down, we utilized a Vortech air-to-water aftercooler. The fuel system consisted of a set of 810cc injectors fed by a modified AEM billet fuel rail and Aeromotive adjustable fuel-pressure regulator. We continued the use of the Hondata to control the fuel and timing tables.
The ignition system consisted of a stock Honda distributor augmented by a Crane HI-6 ignition amplifier and a set of Denso Iridium spark plugs. Also present was a Holley 68mm billet throttle body, a custom 3-inch dyno exhaust and a full array of boost, exhaust gas temperature and inlet temperature sensors.
It is always a good idea to have as much information as possible when running high-power turbo motors on the dyno. The data logging helped provide information on the boost pressure versus exhaust back pressure, the temperature of the exhaust after the turbo (EGT) and even the inlet charge temperature before and after the Vortech aftercooler. A custom discharge tube was fabricated to connect the outlet of the turbo to the inlet of the air-to-water aftercooler.
The motor was treated to a break-in procedure before subjecting it to any hard pulls under boost. Once we were convinced that the rings and bearings were all seated properly, we began tuning and slowly upping the boost pressure. The boost was controlled by an A’PEXi electronic wastegate controller, which allowed us to dial in the desired boost pressure. The Hondata was employed to control both the timing (set at 20 degrees total under boost) and the air/fuel curve supplied by the 810cc injectors.
After playing with the Skunk2 adjustable cam sprockets, we were ready to up the boost pressure. Running a peak boost pressure of 6.9 psi, the 1.93-liter motor produced 336 hp. Upping the boost pressure to 9.3 psi resulted in a jump to 382 hp. The next step brought 12.1 psi and 431 hp, followed by 14.2 psi and 475 hp. We had just reached the power level of the smaller turbo B16A with 7 or 8 psi less boost—things were looking promising. Jumping up to 61.2 psi brought 500 hp, while 18.7 psi took us to 539 hp.
It should be noted that all of these runs were made with just 20 degrees of total timing and a very safe air/fuel mixture of 10.2:1 (using 114-octane Union 76 race fuel). Jumping up to the same boost level as the B16A (22 psi) brought 607 hp and over 400 lb-ft of torque. We had officially reached our 600hp goal using the same boost level as the smaller 475hp B16A. Just for fun, we cranked up the boost one more time to 25 psi and managed to coax an amazing 656 hp and 428 lb-ft of torque from our turbo 1.93-liter!
While running the 656hp turbo motor on the dyno, we noticed that the boost response seemed to be a little sluggish. We initially attributed this to the large GT72 turbo, but our concerns about the response rate were verified after removal of the motor from the dyno. Upon disassembly, we discovered that the turbine impeller had been damaged during testing. The culprit turned out to be a small section of the exhaust gasket located between the exhaust manifold and the turbine housing. Apparently, the gasket overhung the turbine housing slightly. This overhang was eventually worn away by the hot exhaust gases, sending the heated laminate gasket through the turbine side of the turbo. The result was damage to the impeller wheel.
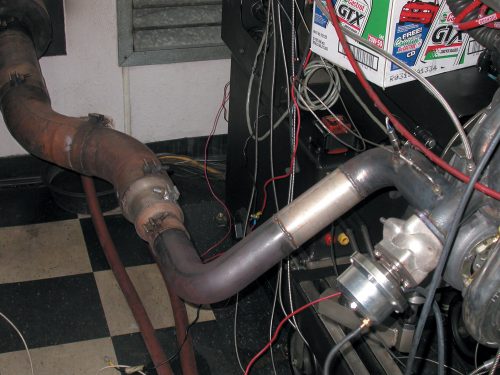
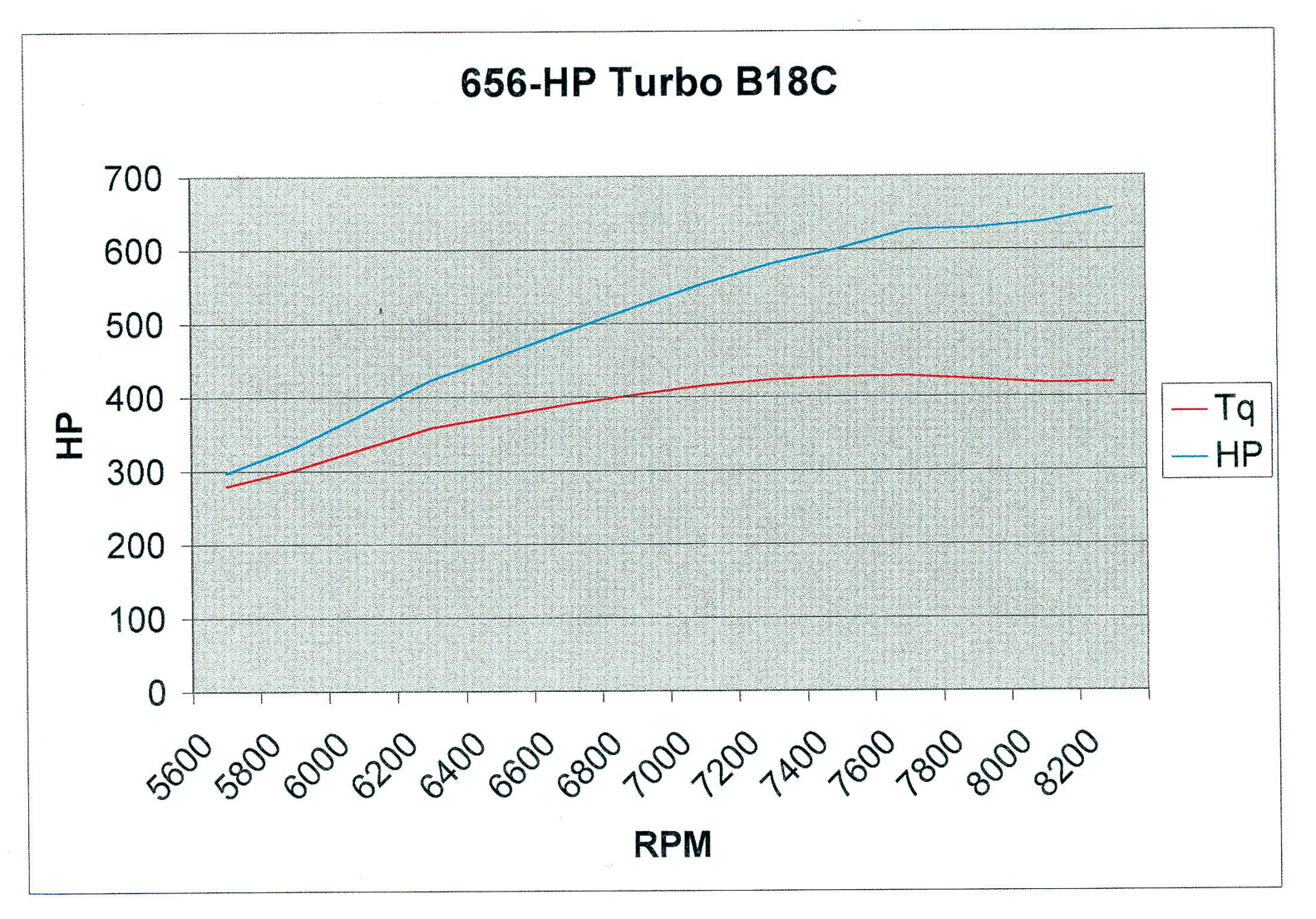
One thing that should be obvious from the graph is that our damaged turbine impeller was limiting boost production until nearly 6,500 rpm. Having run a number of turbo motors in the past, we know that full boost (on the loaded engine dyno) is usually obtained well before 6,500 rpm, even using a large turbo like the GT72. Still, 656 hp from just over 1.9 liters is pretty impressive. The air-to-water aftercooler made sure our charge temps were kept cool even with 25 psi showing on the boost gauge. Running ice water through the core allowed us to lower the inlet charge temps by a whopping 238 degrees (from 335 degrees down to just 97 degrees).
It is amazing that the turbo worked at all, but the damaged turbine wheel allowed exhaust pressure to bypass the wheel. It took a great deal of flow to finally coax the wheel to deliver boost pressure. We expect that a new wheel would greatly improve response and suspect that it might also improve the peak power at a given boost level. But for now, we are quite happy with our production of 656 hp at 25 psi.
Article Sources
Coast High Performance
310/784-2977
115 E Gardena Blvd #1b, Gardena, CA 90248
Ferrea Racing Components
888/733-2505
2600 N.W. 55 Ct. Ste. 238 Ft. Lauderdale, FL 33309
Holley Performance Products
270/782-2900
1801 Russellville Rd. Bowling Green, KY 42102
Innovative Turbo Systems
805/526-5400
845 Easy St. Unit 102 Simi Valley, CA 93065