Street Rods
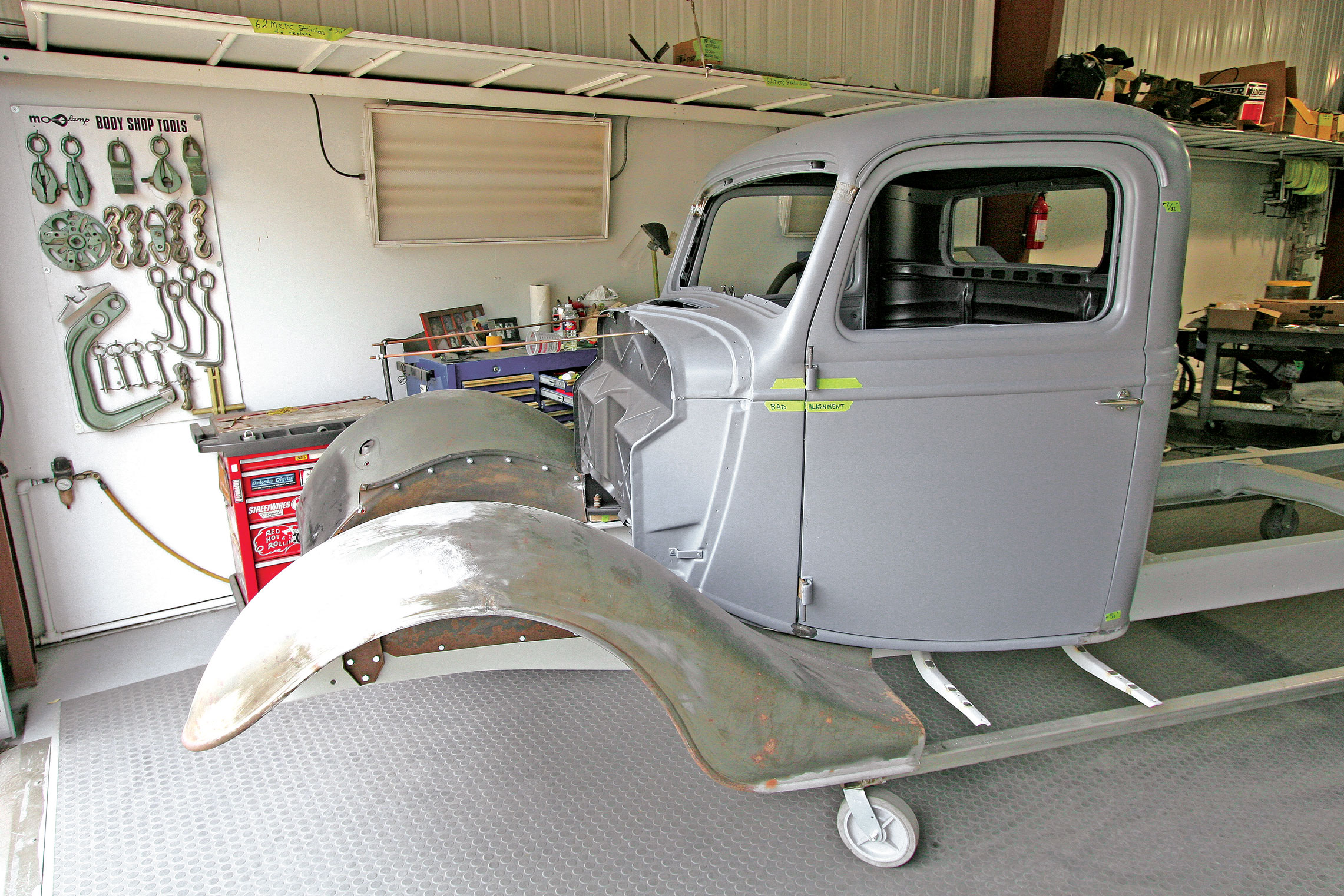
Pickup trucks from the ’30s were never meant to be high-quality hot rods, but several builders, including Jeff Lilly Restorations, are ready to change that theory. Lots of beater trucks are being built and driven frequently, and it’s great to see some of the cool ideas that come from these old farm or service trucks. Pickups are hot right now, and while some rodders are using low-gloss paint for their final coatings, many opt for a super-slick appearance with precision gaps and laser-straight panels.
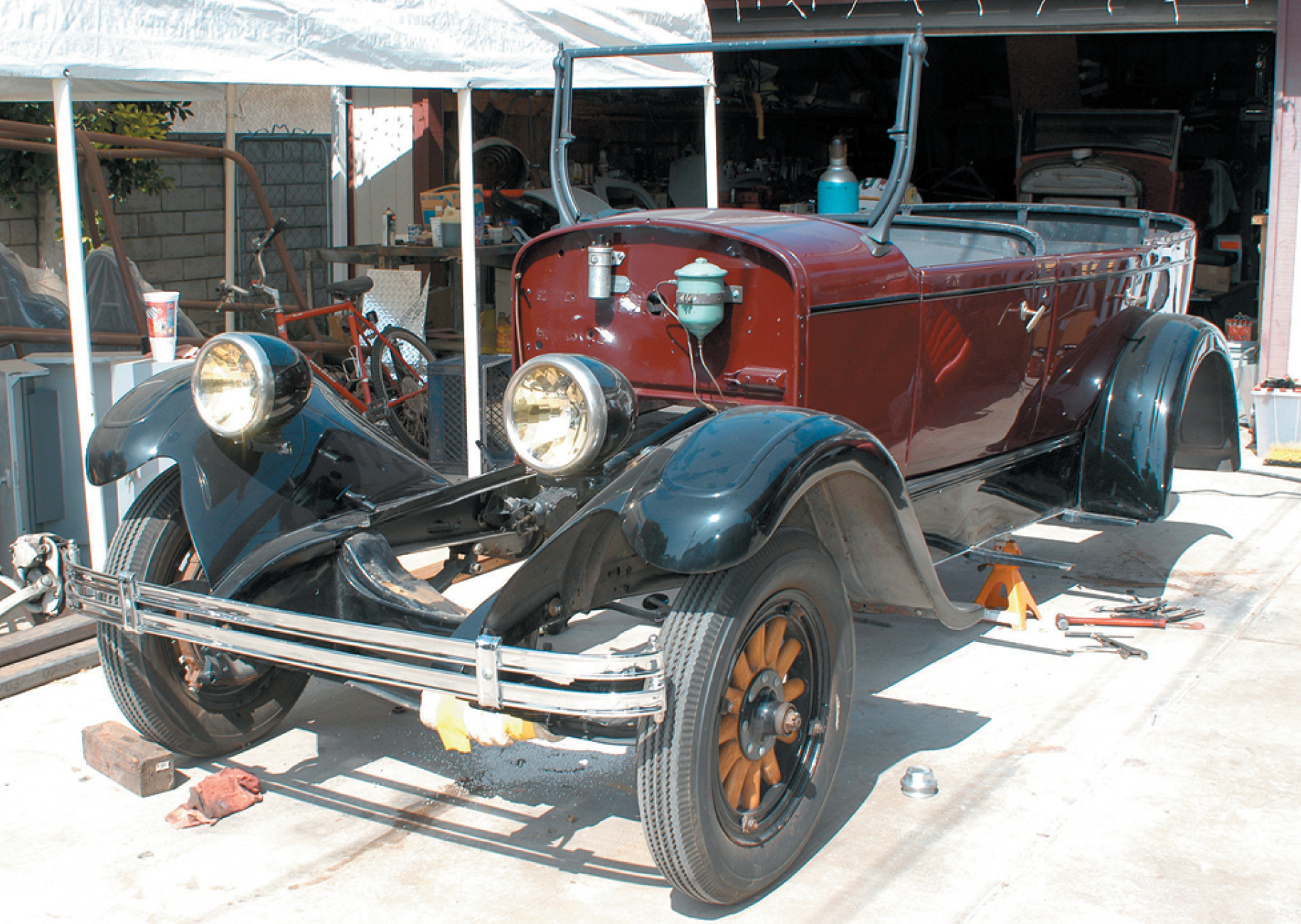
Tom Lawson was attending the Goodguys West Coast Nationals with his family and friends when a friend of his father-in-law, Bill, also a street rodder, walked up and started talking to everyone in the group.
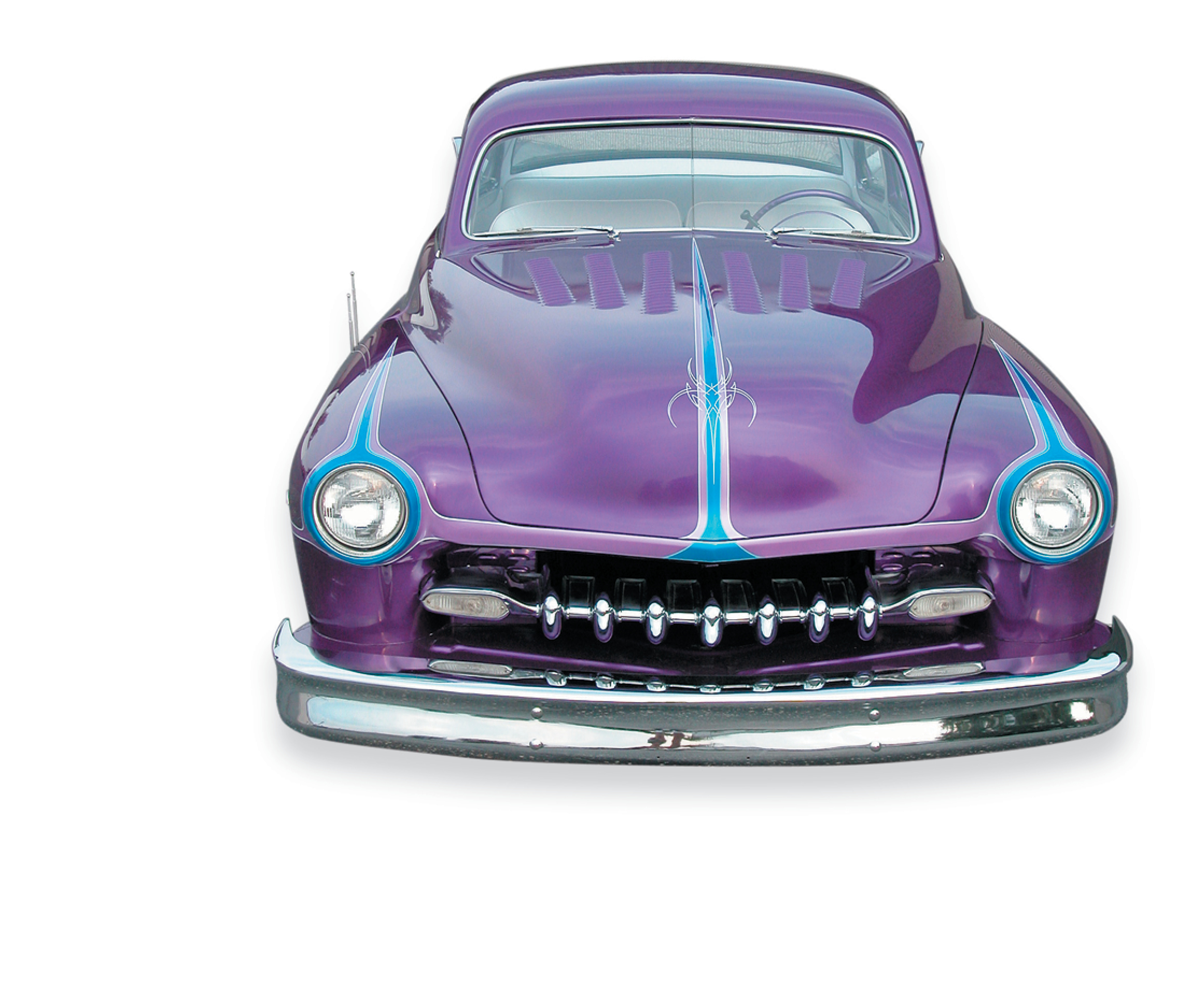
Sketch out a few ideas on paper, or some people like to put tracing paper over an actual photograph. Somehow come up with a plan for your paint scheme. We opted to “visually lengthen” the car by using a base scallop to connect both sides. This pattern flows to the side chrome, and extending this outline from the front to the rear gives the longer appearance. The stock Mercury body is thick. By putting the scallops below the trim line on the car, your eye is automatically drawn downward, giving the Mercury a lower, thinner appearance.
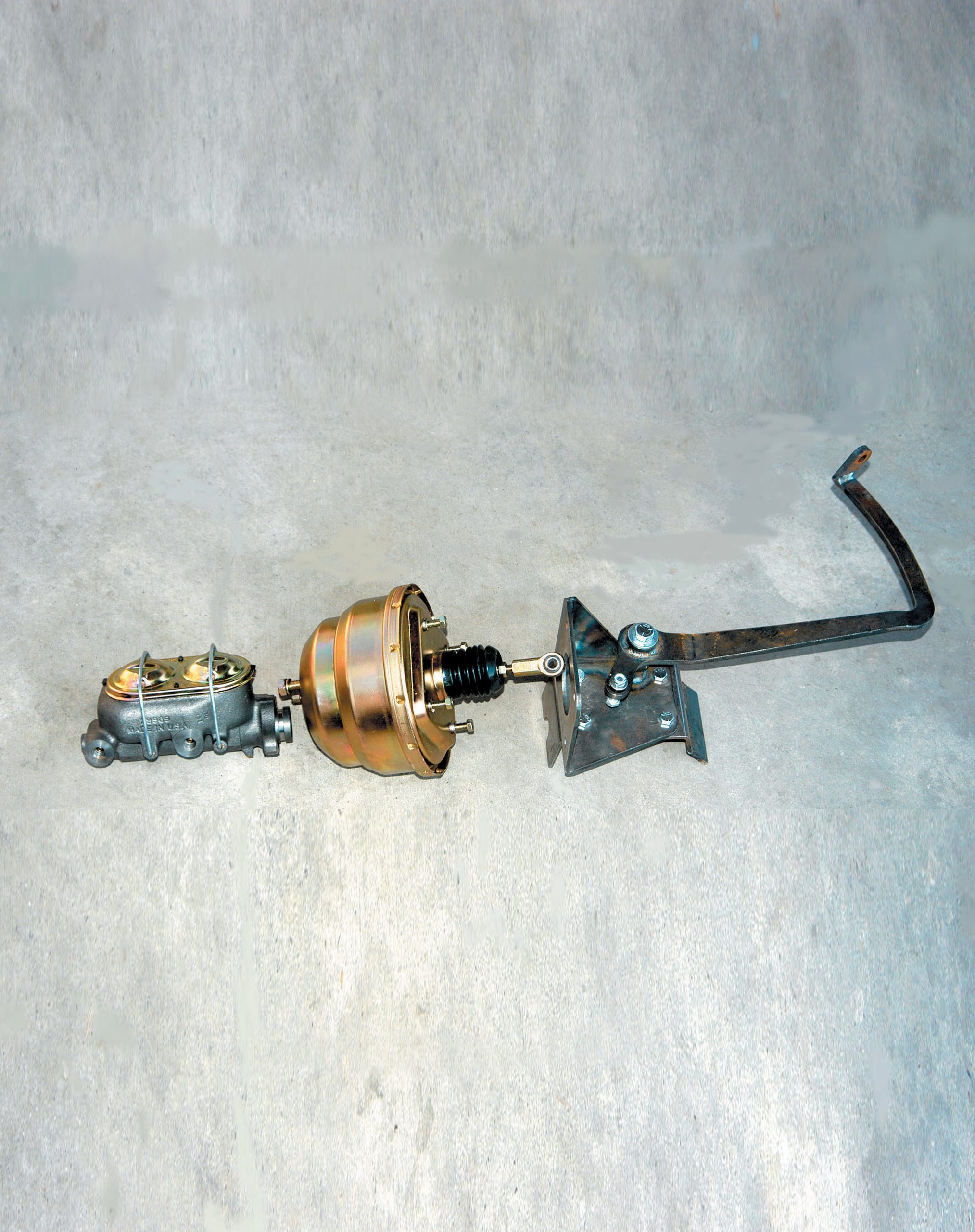
If you own a Ford or Chevy, most of the parts you will need to build a street rod are readily available, and from a variety of suppliers. We have written numerous stories about kits for these cars in our family of rodding magazines, and some of them were a direct replacement for the original. By and large, they worked perfectly and bolted right in, as designed. These types of kits are convenient for many street rod builders, as well as street rod shops, and they are part of what has helped grow our hobby into such a broad special-interest group. But in addition to the “normal” and most popular rods, there were many other great cars made in the pre-war era, and some of them can be a real challenge to street rodders because there are no pre-manufactured parts, and no kits that make them easy to build. Sounds like the old days, right? Well, that’s the modern world for you–even our hobbies have become targets of convenience.
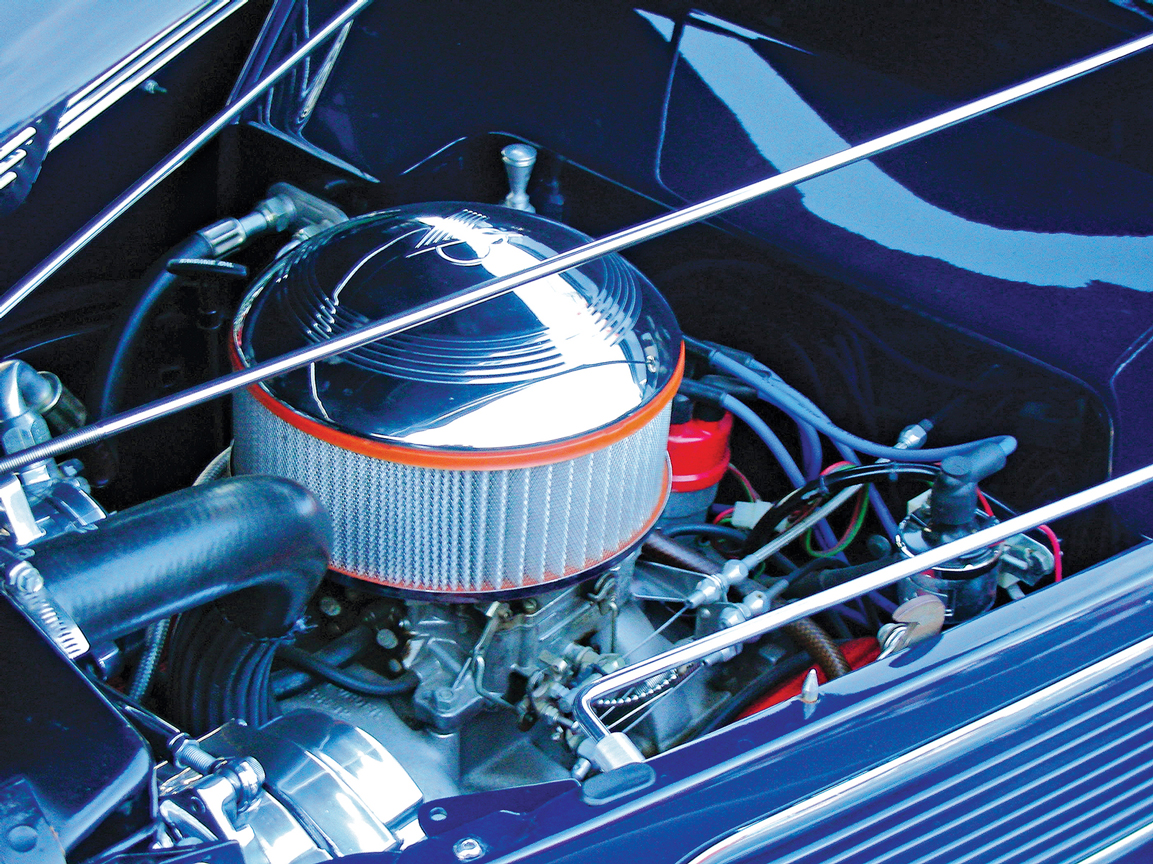
Call ’em tech tips, building tips, details or whatever you like, but this is the stuff we see at events and shows while shooting features or doing shop tours, not to mention things we’ve discovered while working in our own shops. It’s like when you’re foot-cruising an event with the boys and pointing things out to each other, or when you have a stroke of genius while working on your own project.
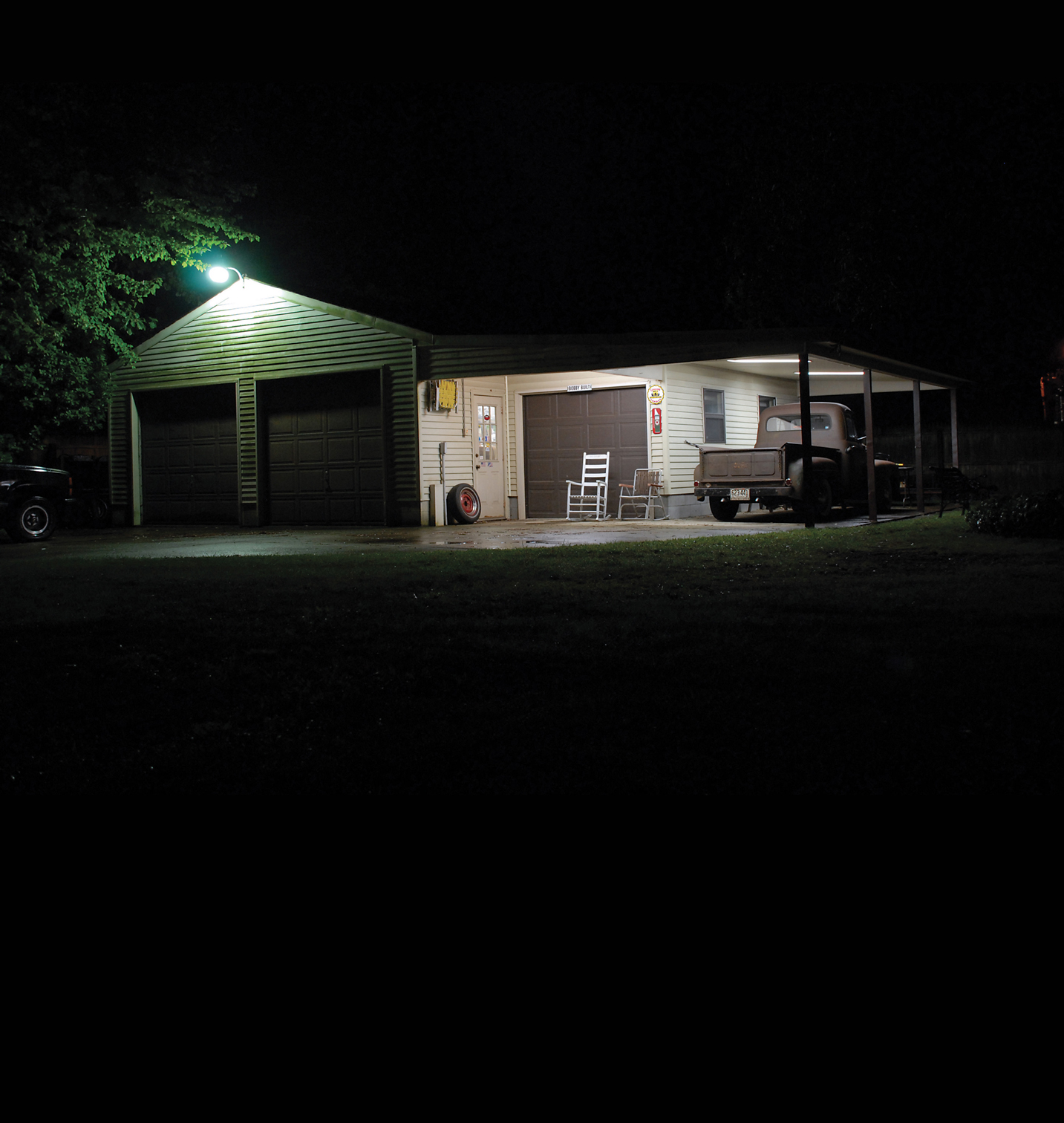
We always find it amusing when a bench racing session turns to building street rods. It seems there is a huge contingency of rodders and observers of street rodding who believe that every car in the fairgrounds area was built by a professional shop. We’re not about to argue the point that a lot of people now pay to have work done on their cars, whether it’s chassis work, bodywork or upholstery. However, there is still a large group of people who spend evenings and weekends out in the garage forming brackets, repairing rust, blocking panels and wiring hot rods. In short, they are building cars the old-fashioned way—at home with the help of a few friends.
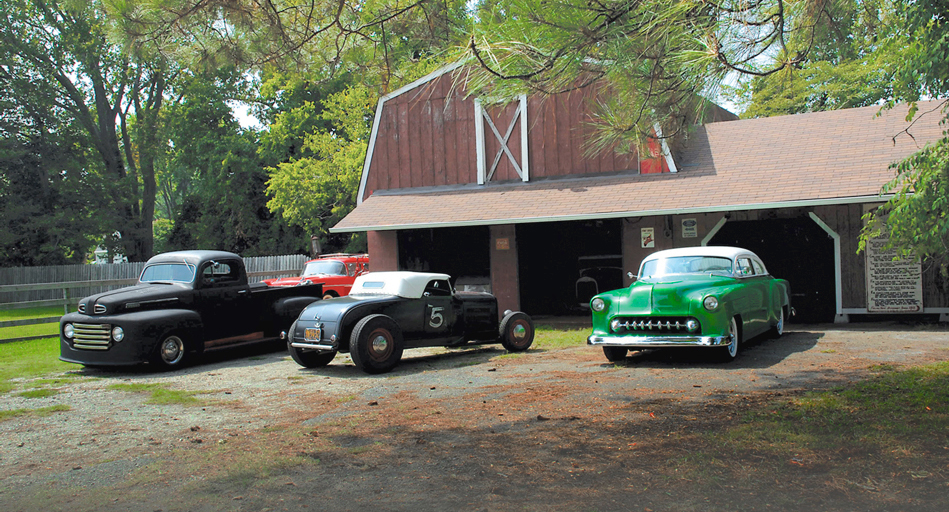
Jack Fuller has been at this hot rod game for a long time, and while he builds hot rods for a living, make no mistake—this is a man who loves his work. As a matter of fact, the mantra of the garage is, “When the fun stops, the doors close for good.” It’s pretty simple stuff, and oddly enough, that seems to be the specialty of the house—basic hot rods that look cool and work well. Jump in a Jack Fuller hot rod, and you’ll know it was designed to be driven. Jack’s own ’32 cabriolet has seen untold miles over the years, as have most of the other hot rods he has built.
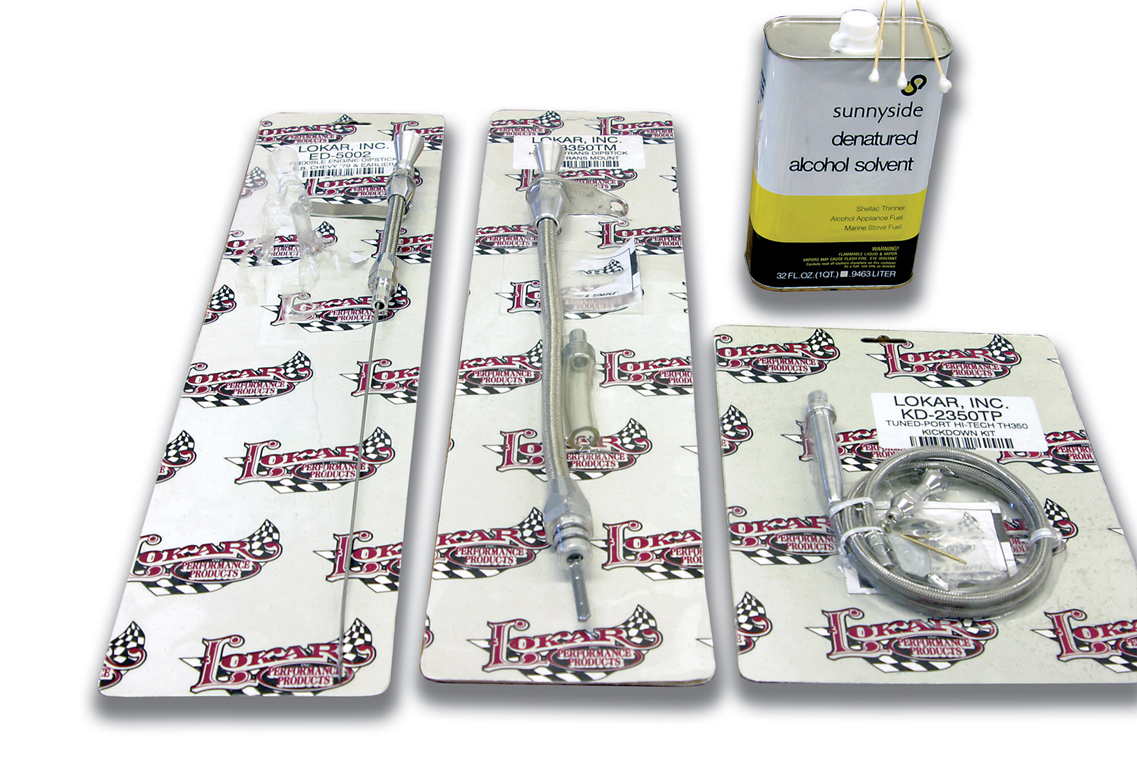
Fluids are the lifeblood of the vehicle. We need to contain those fluids yet still be able to monitor the fluid levels. Our older readers can remember the days before aftermarket flexible dipsticks or silicone caulk were available. The only option in those days was to use an OEM dipstick and dipstick tube. If you needed to shorten the tube, a hacksaw was the tool of choice. If you cut 4 inches off the tube, you then cut 4 inches off the dipstick and ground a couple of notches in the side of the dipstick to note “full” and “add.” Gaskets could be sealed with Permatex, but they had to be used as there was no such option of placing a bead of silicone caulk on the mating surface and assembling the parts.
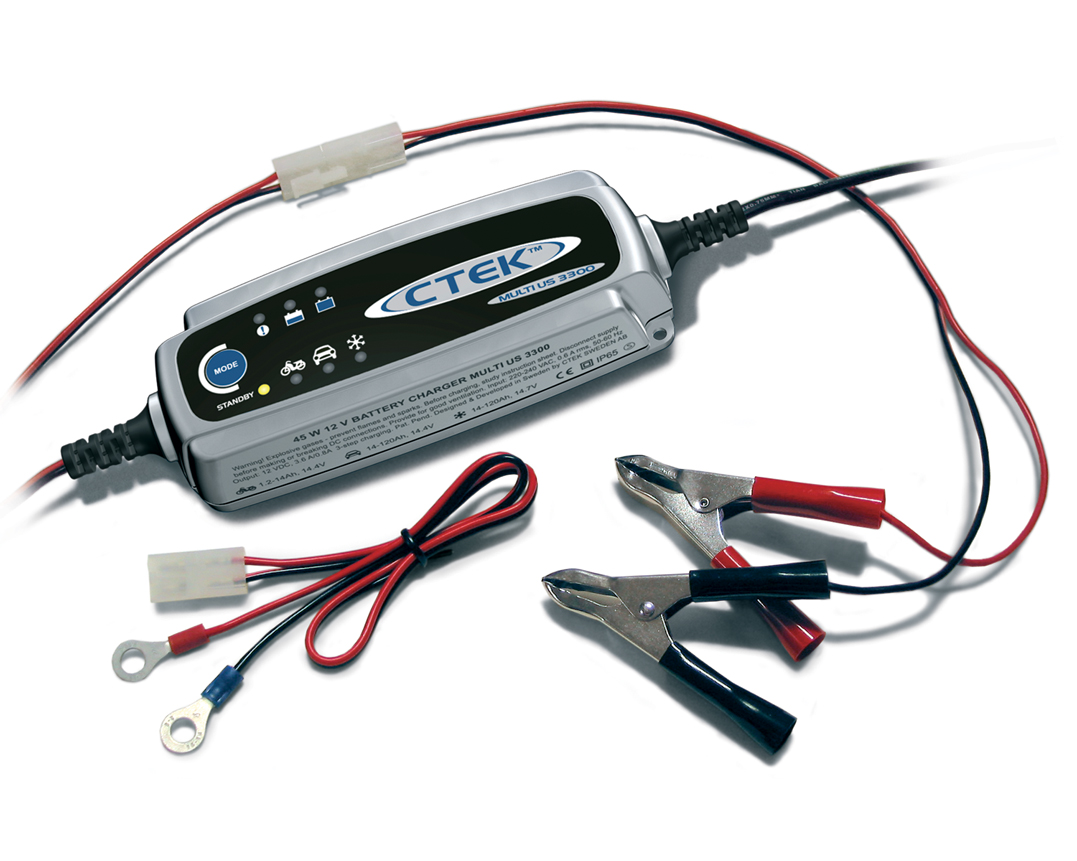
If you are going to connect anything automatic to your car, especially when dealing with electricity, lead and acid, you owe it to yourself to do a bit more research rather than pulling just any super-discounted, off-the-shelf item and connecting it to something as potentially volatile as a lead-acid battery. But we have, haven’t we?
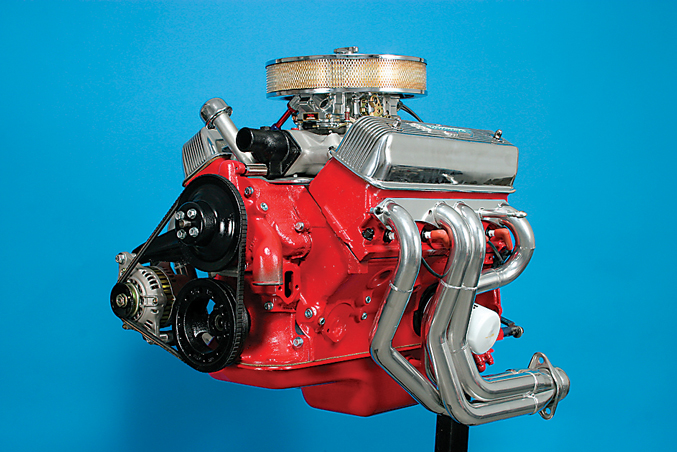
When Ford introduced its Y-block engine in 1954, it labeled the engine the worthy successor to the venerable Flathead. The Flathead gained a loyal following of hot rodders and racers, but the big Cadillac overhead-valve V-8 and Oldsmobile’s Rocket 88 were stealing Ford’s thunder in terms of power, so something had to be done, and Ford decided to respond. The answer was a clean-sheet V-8 design, featuring overhead valves and improved cooling compared to the old Flathead. It was dubbed the “Y-block” because of the way it looked and because of its deep skirt and tall cylinder heads.