Chassis
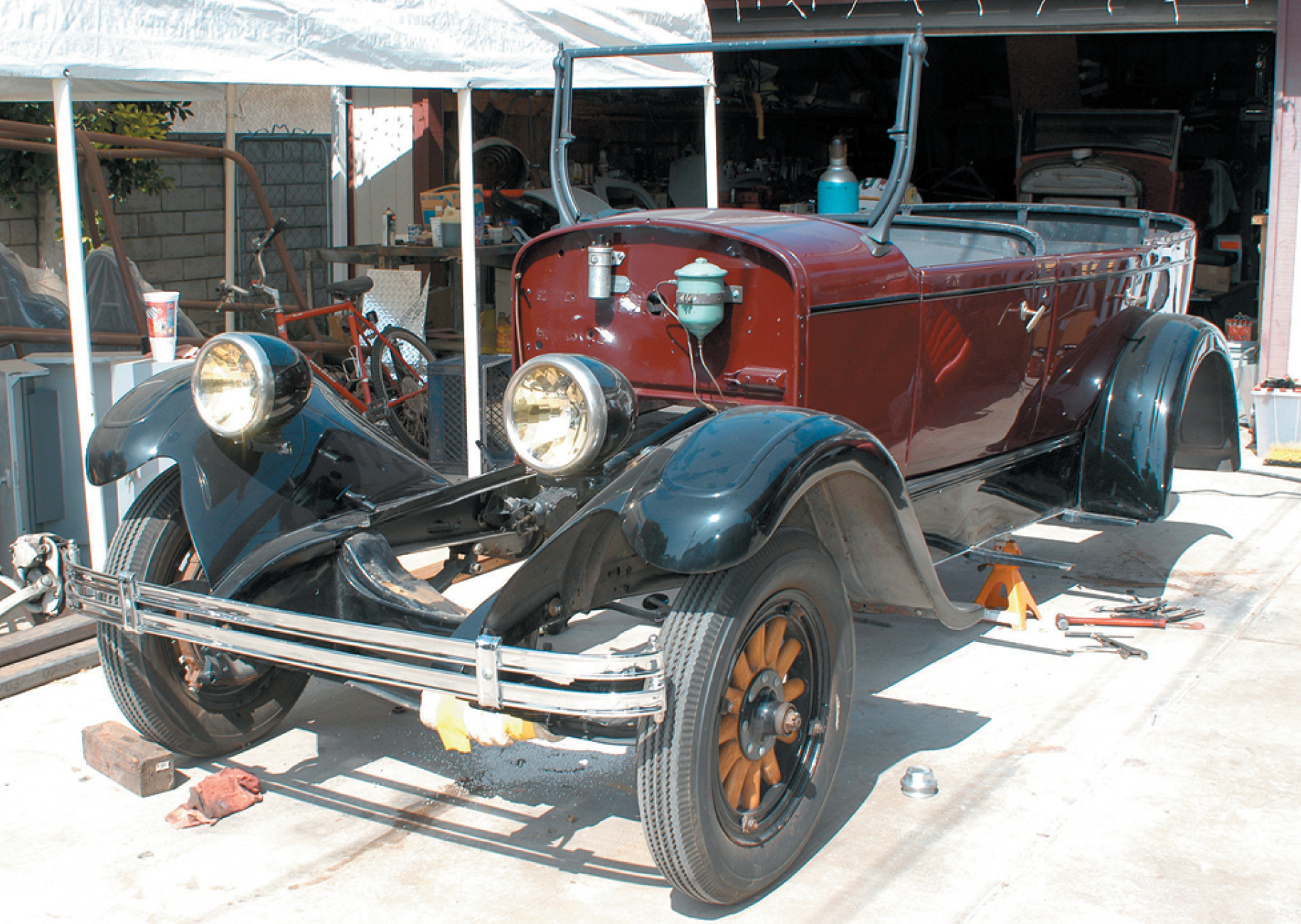
Tom Lawson was attending the Goodguys West Coast Nationals with his family and friends when a friend of his father-in-law, Bill, also a street rodder, walked up and started talking to everyone in the group.
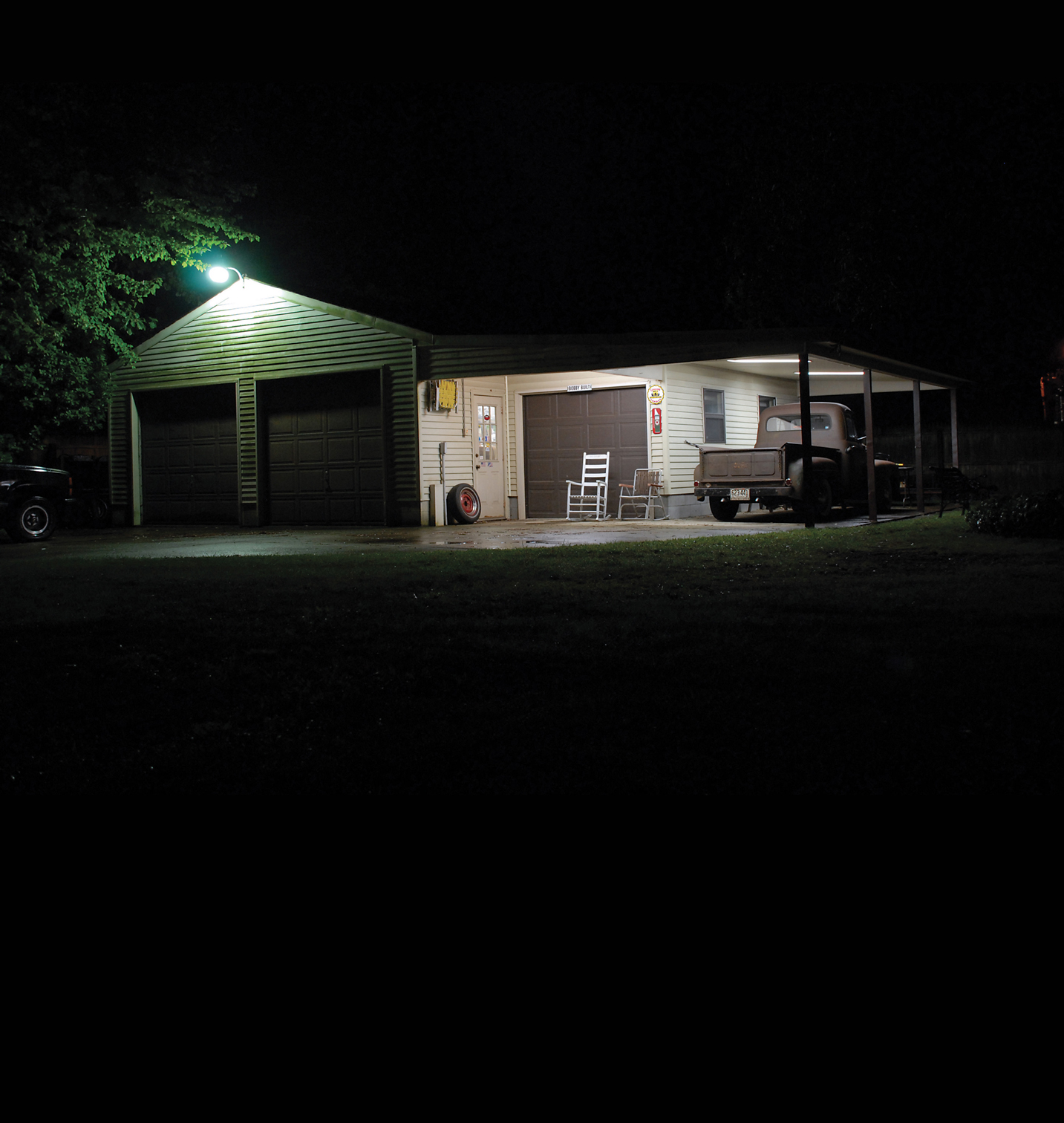
We always find it amusing when a bench racing session turns to building street rods. It seems there is a huge contingency of rodders and observers of street rodding who believe that every car in the fairgrounds area was built by a professional shop. We’re not about to argue the point that a lot of people now pay to have work done on their cars, whether it’s chassis work, bodywork or upholstery. However, there is still a large group of people who spend evenings and weekends out in the garage forming brackets, repairing rust, blocking panels and wiring hot rods. In short, they are building cars the old-fashioned way—at home with the help of a few friends.
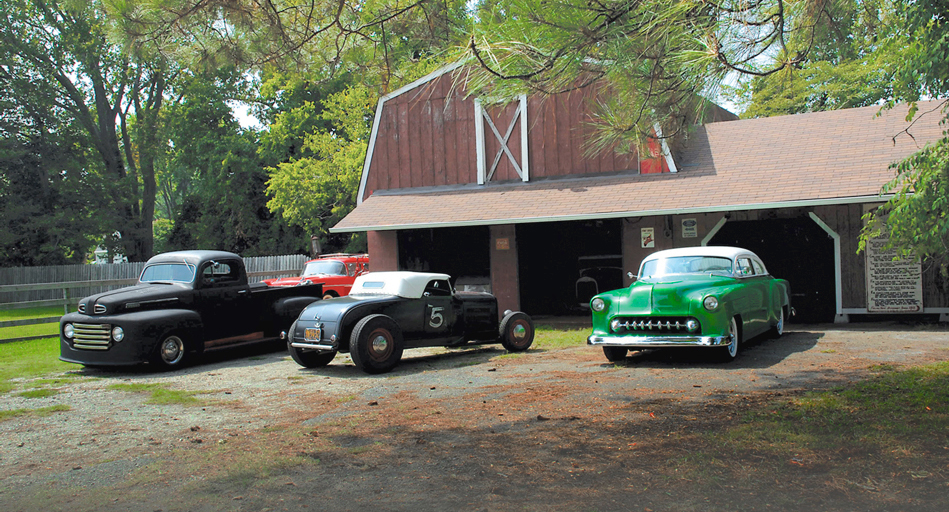
Jack Fuller has been at this hot rod game for a long time, and while he builds hot rods for a living, make no mistake—this is a man who loves his work. As a matter of fact, the mantra of the garage is, “When the fun stops, the doors close for good.” It’s pretty simple stuff, and oddly enough, that seems to be the specialty of the house—basic hot rods that look cool and work well. Jump in a Jack Fuller hot rod, and you’ll know it was designed to be driven. Jack’s own ’32 cabriolet has seen untold miles over the years, as have most of the other hot rods he has built.
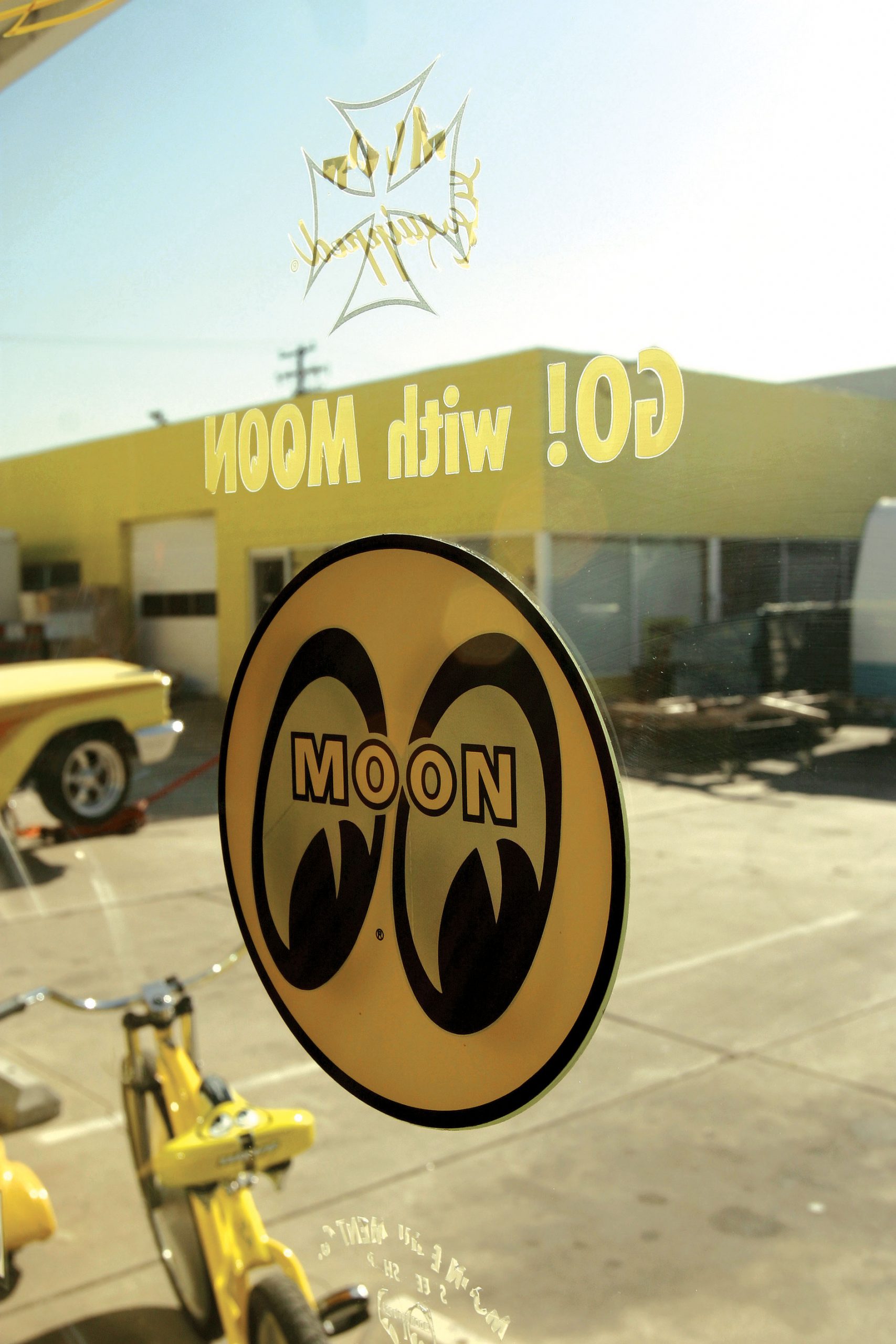
The showroom is what every auto parts store dreams of being: diced in checkerboard black and yellow tile with a heap of pegboard. Up front, the sales counter is the hub of business, fueled by eager customers that keep the phone ringing off the hook. Bob, Sam and Robin deal one-on-one with customers, keeping all 50 states Moon-equipped.
There are many reasons why the icon cars have achieved the lofty status they now enjoy, but one of the more obvious reasons is the simple fact that they were finished. Their existence and subsequent high-level exposure have inspired many a young lad to undertake similar projects, and for every famous car built in the early years, probably two others were started in an attempt to either copy or outdo it, but they never saw the light of day.
For every hot rod shop that has a show on TV, there are countless smaller shops that will never get mainstream TV exposure or clothing lines sold at Wal-Mart. But all across the country, it’s these smaller shops that turn out the majority of the street and super rods that you and I enjoy, and that we see at shows. And even though these little guys may not have big reputations yet, they churn out consistent and excellent work—and, that is precisely how some of these smaller shops will eventually become bigger shops with even more prestige.
“Real hot rods have axles,” or so they say. That was our story, and we stuck to it fondly for more than 10 years. The ’47 Ford sedan delivery we drive came to us with a new Super Bell dropped axle and four-bar linkage professionally installed by Dick Jones’ shop in Campbell, California. It wasn’t really a hot rod; more like a primered beater with no interior, very little glass and enough rattles that a radio was a waste of time. It was a project car for another magazine for several years, and as such was the subject of many tech articles, updating it with all manner of great stuff. But it was still a primered beater, so the axle suited it just fine, and we got many miles of enjoyment out of this setup. Oh, it could have had a nice, new IRS more than once, but it just wasn’t that kind of car.
If you attend car events in California, such as NHRA’s California Hot Rod Reunion in Bakersfield, the West Coast Kustoms show in Paso Robles or the L.A. Roadster Show in Pomona, you will notice that rat rods are a growing segment of the hot rod hobby. Years ago, when they started becoming a common sight at many of the shows, the mechanical aspects of most of the cars were scary at best. You could see cars with no springs, some without floorboards, and many constructed with less-than-desirable stick welding. It is this type of construction that created the name “rat rod.” Fortunately, over the past few years there has been an attempt to upgrade the construction of rat rods, even though the enthusiasts want to use as many original parts as possible.
When building a street rod there are a great many facets of the construction process that go into making the car an award-winning creation. First, there’s planning. The planning of the car can and should include attention to each and every area of the car, from concept to reality. Even the most basic of projects should have the proper planning involved, no matter what the final product might be. Once work has begun on the project, countless hours are generally involved in attending to every detail. From making the many modifications to the chassis to attain the desired drive train, to the matching and mating of the different components together, this becomes an involved process requiring a great deal of skill in fabrication and engineering.