Dyno Testing Tri-Y And 4-Into-1 B16A Headers
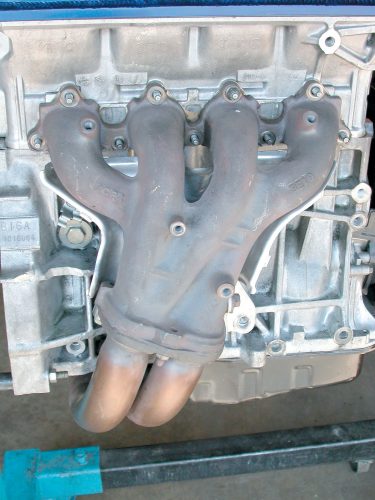
When it comes to performance, there is one steadfast rule: All the good air that goes into making horsepower must eventually find its way out. This means that adding all the cool camshafts, intake manifolds and even superchargers to help improve airflow into the motor will be useless (okay, maybe not useless, but certainly much less effective) if the motor is not able to rid itself of the exhaust. Cork up a serious performance motor and watch it struggle and gag on its own exhaust fumes.
Adding the right header can add much-needed exhaust flow and additional power through a process called scavenging. You see, a header is much more than a simple set of tubes welded together to direct the exhaust flow. A true header provides not only a direction for the exhaust, but can also help draw spent gases out of the combustion chamber. The effectiveness of this so-called scavenging effect is determined by a number of design criteria, something we hope to test in this article.
When it comes to headers, there are basically two primary designs: Tri-Y and 4-into-1. As the name implies, the Tri-Y design refers to a series of three Y sections created by joining the primary tube of runner 1 with runner 4 and runner 2 with runner 3. The four runners converge into two tubes when they merge to form the final Y section to complete the Tri-Y design. In the case of the Tri-Y header offered by Airmass, the final Y section is merged to form a short collector.
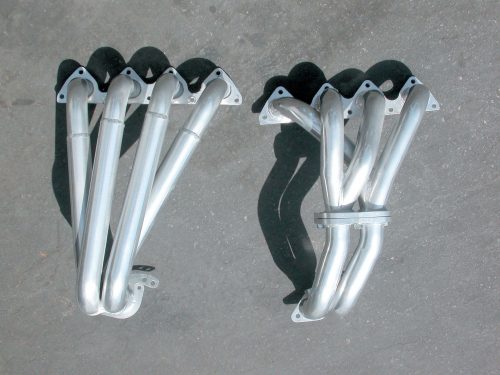
By contrast, the 4-into-1 header features no Y sections, but rather four runners that merge into one common, final collector. There are short versions of the 4-into-1 design and there are those with longer primary tubes. The Airmass header features long primary runners to help enhance low-speed and mid-range power production. In theory, the 4-into-1 header should offer more top-end power, while the Tri-Y header is designed to bolster mid-range torque. Though there is a great deal more to the performance of a header than the overall design (4:1 vs. Tri-Y), this test indicates that the basic layout is a strong indicator as to the eventual performance. However, do not misinterpret an absolute power number on one combination and expect that it will translate to another more powerful one.
Before we get to the test motor and results of this comparison, we should take a closer look at additional design criteria that may also affect power output. Within each design, a number of variables can be changed to alter the eventual performance torque and/or horsepower. With either design, it is possible to change the diameter of the primary and collector tubing. With the Tri-Y, add to that the diameter of the secondary tubing. In addition to tubing diameter, it is also possible to change the length of the primary pipes prior to their merging to form the secondaries (or collector, in the case of the 4-into-1). The same is true of the length of the secondaries and especially the collector.
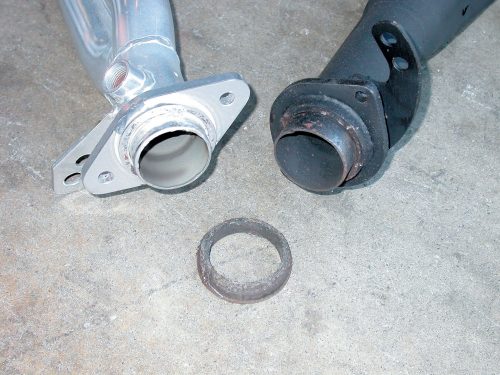
Speaking of collector, it is possible to alter not just the length and diameter, but also its shape. The collector can be tapered, converging or even diverging on the exit and the exit diameter can be altered as well.
By now it should be obvious that a great many possibilities exist when it comes time to design a header. Throw in the near infinite number of varying engine combinations—even with just one engine family, such as the B-series Honda—and you can well imagine how difficult it can become to build a header that works the best on all applications. It’s nearly impossible.
It is for this reason that Airmass offers both designs, Tri-Y and 4-into-1, as each design has its pluses and minuses. What better way to demonstrate the tuning effect offered by each header design than to compare them on the same motor?
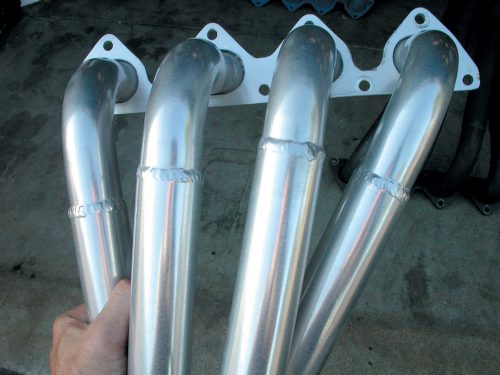
To properly test not only the header designs, but also the stock exhaust manifold, we assembled a rather basic B16A test motor. The B16A was chosen for its availability, as it is much more prevalent than the B18C (GSR) or B18C5 (Type-R) and we wanted a healthy motor that was both powerful and representative of what might be run on a typical street Civic.
The mods were minimal, consisting of replacement forged JE pistons and Probe Racing forged connecting rods. The forged short block was topped off with a hand-ported and slightly milled cylinder head and a set of 57100 Comp cams with Crane adjustable sprockets. A Holley 68mm throttle body and a set of 30-pound injectors relied on an Aeromotive adjustable fuel-pressure regulator to control the fuel pressure. A Hondata programmable ECU was employed to dial in the air/fuel and timing curves. The dyno exhaust consisted of a 2.5-inch section of tubing connected to a 3-inch, 90-degree elbow, and finally out to a 6-inch evacuation tube. All three of the headers (including the factory header/exhaust manifold) were run through this dyno exhaust system.
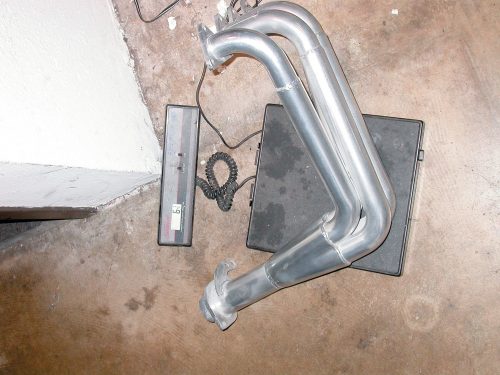
We first ran the B16A test motor with the stock exhaust. The B16A produced 195 hp at 7,700 rpm and 139 lb-ft of torque at 7,200 rpm. Thanks in part to the torque-producing nature of the stock Tri-Y design, the little B16A produced over 130 lb-ft. of torque from 5,200 rpm (the engagement point of the VTEC cams) to 7,900 rpm. Our mildly modified 1.6-liter B16A was pumping out as much power as a 1.8-liter Type-R Integra motor—with the stock exhaust, no less.
Next up was the aftermarket Tri-Y header from Airmass. The first thing we noticed about this header was its lighter weight compared to the stock manifold setup. Our handy UPS scale told us that we saved 15 pounds by replacing the heavy cast-iron exhaust manifold. After comparing the stock Tri-Y manifold to the Airmass Tri-Y header, we began to wonder just how much power the header had to offer, as the two designs were so similar.
Our fears were soon put to rest after the very first dyno pull showed power readings exceeding 200 hp. Equipped with the Airmass Tri-Y header, the B16A produced 201 hp at the same 7,700 rpm and 141 lb-ft at 7,200 rpm. Note that both the stock manifold and the Airmass Tri-Y header produced horsepower and torque peaks at identical engine speed (7,700 rpm and 7,200 rpm). Though cam timing and intake design play major parts in shaping the overall power curve, identical power peak engine speeds show—at the very least—a strong consistency in the exhaust design.
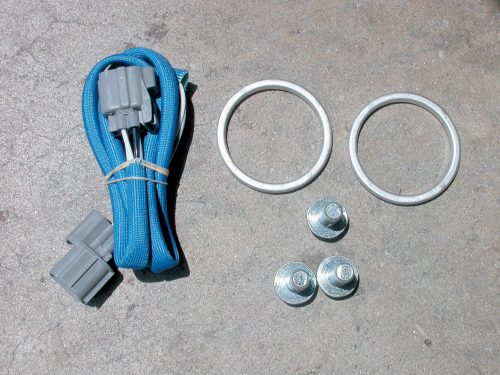
The similarity in design didn’t stop the Airmass header from getting the better of the stock manifold, especially once the revs reached 6,000 rpm. From 7,500 rpm to 8,100 rpm, the Airmass was up by 5 hp to 7 hp and nowhere in the rev range did the Airmass Tri-Y lose out to the stock exhaust manifold.
After seeing the gains offered by the Tri-Y header, we were anxious to see how well the Airmass 4-into-1 header would perform. Performing a header swap is no big deal; even installing a single-piece 4-into-1 header is not terribly difficult. A skilled enthusiast with reasonable mechanical skills can knock it out in something less than an hour. On the engine dyno, a header swap takes all of five or six minutes, which is why we chose to run the tests on the engine dyno in the first place.
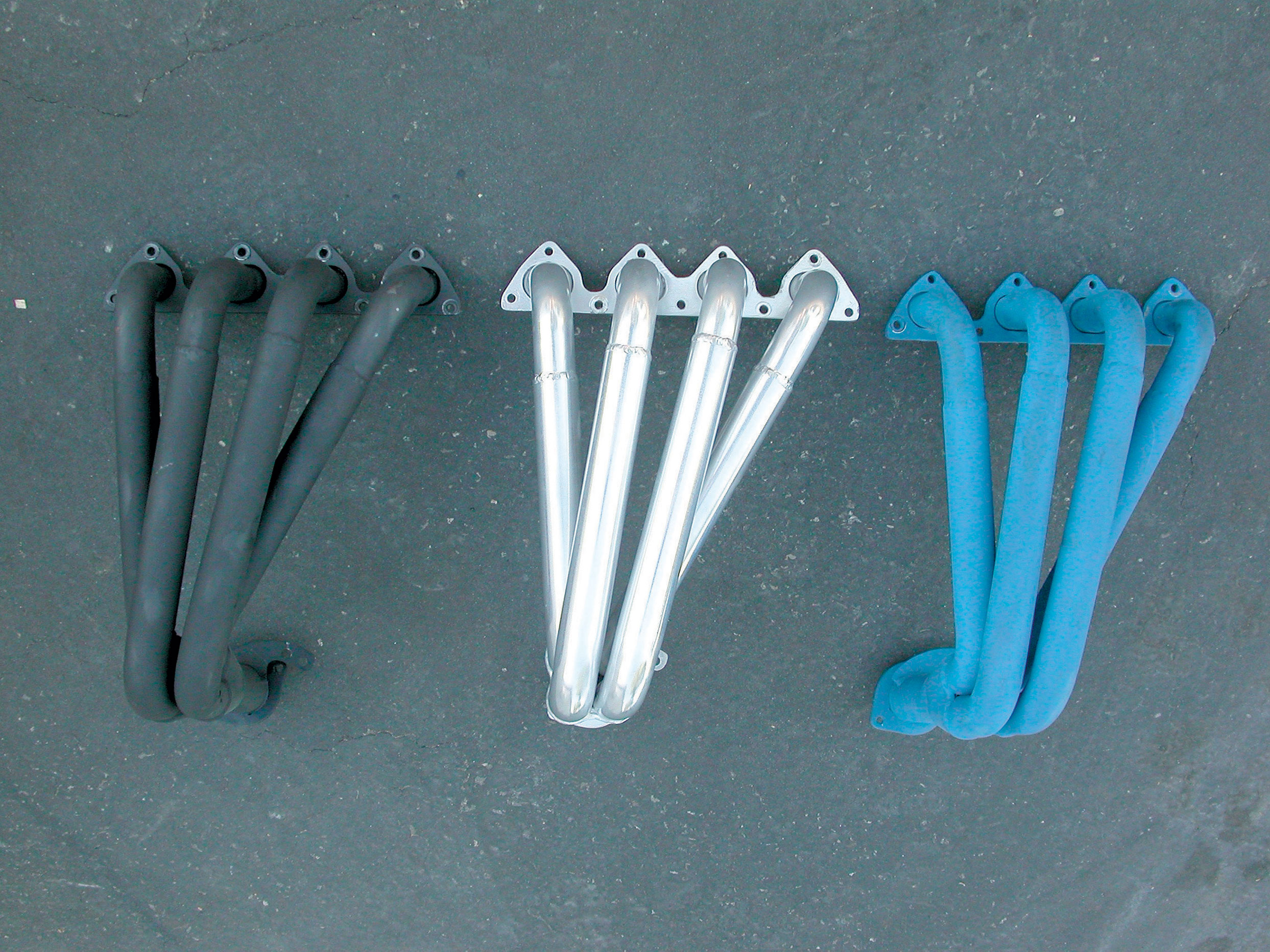
The 4-into-1 header was well worth the six-minute install time, as it posted the best peak power numbers of the afternoon. Equipped with the 4-into-1 header, the B16A produced 204 hp at 7,700 rpm and 143 lb-ft at 7,200 rpm. The 4-into-1 header was worth 10 hp compared to the stock exhaust manifold, but the additional peak power came with a slight penalty down near the VTEC engagement point of 5,200 rpm. The 4-into-1 design was down 3-4 hp for a 600rpm spread (5,300 to 5,900 rpm) compared to the stock exhaust manifold; but by 6,000 rpm, things had turned around and by 7,000 rpm, the 4-into-1 pulled away handsomely.
Whether you choose the 4-into-1 or the Tri-Y, either design offers significant power gains compared to stock.
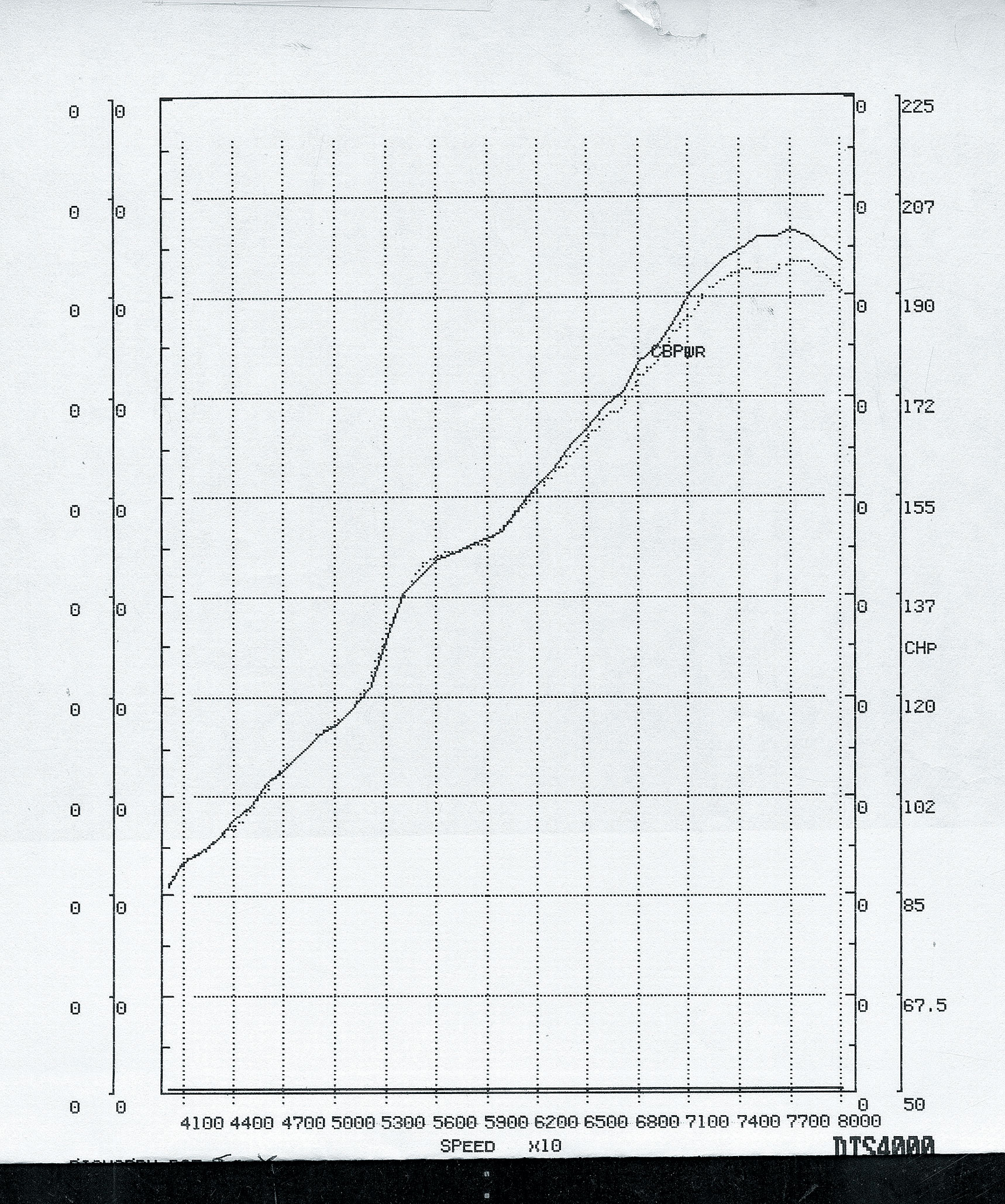
Given that the stock exhaust manifold was a Tri-Y design, it is not surprising that the power curves were similar between the stock and Tri-Y Airmass header, at least until 6,200 rpm. From 6,200 rpm on up the Airmass header proved its worth, besting the stock exhaust manifold by 6-7 hp. In addition to the increase in power, adding the Airmass header knocked 15 pounds off the curb weight. In the all-important power-to-weight ratio, less weight is the same as more power.
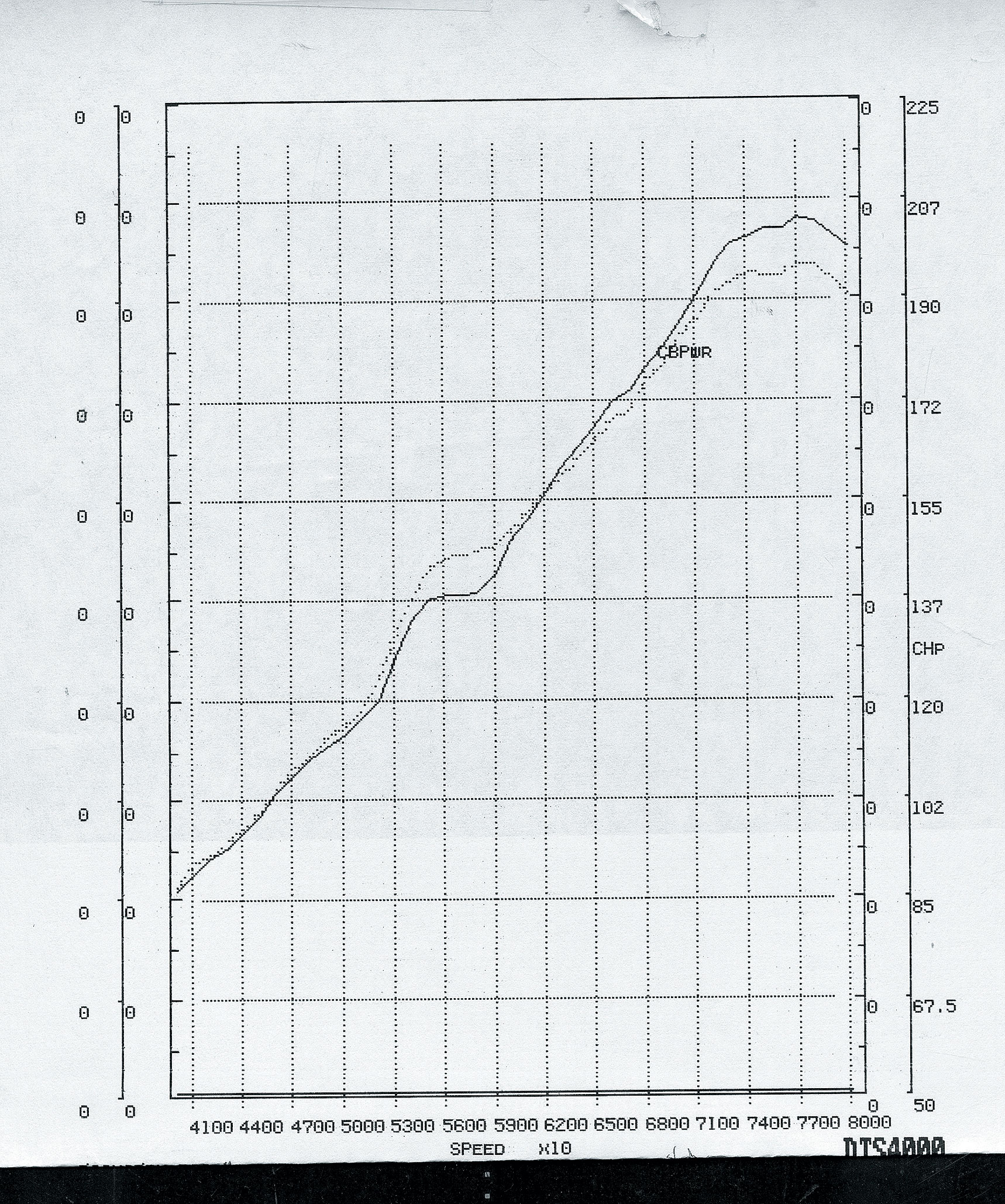
The 4-into-1 Airmass header offered even better peak power than the Tri-Y design—204 hp vs. 201 hp—but as one would expect, the penalty for the extra top-end power was a slight loss in mid-range torque, as that is where a Tri-Y design works best. The peak power gain was a solid 10 hp (over stock) at 7,700 rpm, but the tradeoff was 3-4 hp at 5,400 rpm. If kept in VTEC, the trade would be well worth the extra top-end charge, since the 4-into-1 header offered more power than the stock manifold from 6,200 rpm to 8,200 rpm on our 200hp B16A.
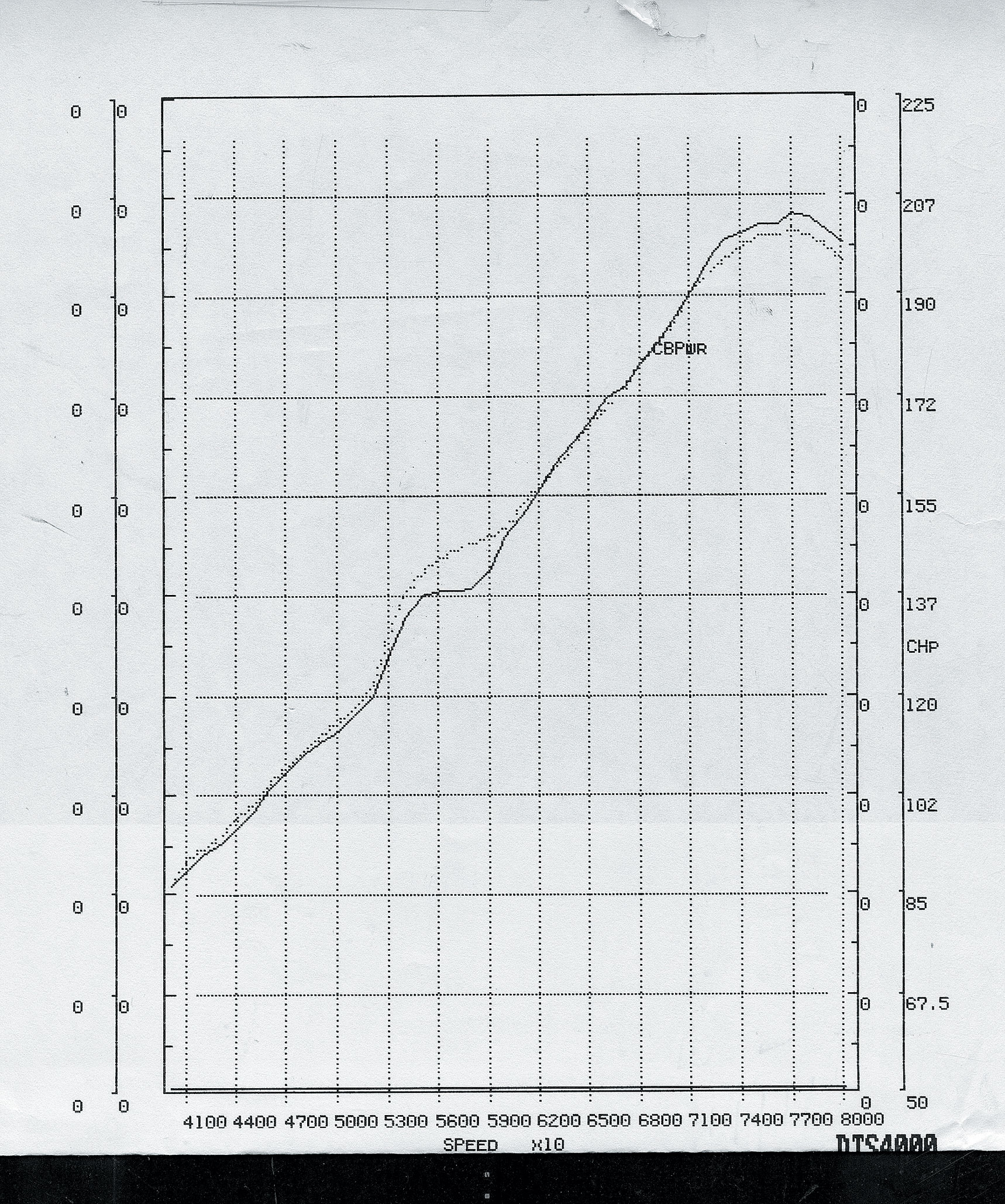
A comparison of the Tri-Y and 4-into-1 Airmass headers showed a similar scenario. The Tri-Y outpowered the 4-into-1 from 4,000 rpm to 6,000 rpm. From 6,000 rpm to 7,100 rpm, it was pretty even, with the 4-into-1 taking over from 7,100 rpm to redline. This comparison would be too close to call in terms of outright acceleration, as the Tri-Y would certainly get the jump out of the hole. Would the top-end charge offered by the 4-into-1 be enough to overcome the torque gains offered at the VTEC engagement point? For street use, we would recommend the Tri-Y design, but for ultimate performance or drag racing, the 4-into-1 design is the way to go. And this would be more true the more powerful the engine. Either way, both designs offered significant improvements over stock, to say nothing of the weight savings.